Fired Heaters
Furnaces are a vital part of many refinery units. In Bottom of the Barrel processing units, such as Delayed Cokers, Visbreakers, Resid Hydrocrackers or Vacuum Distillation units, the build up of solid coke residue reduces heat transfer and increases fuel consumption & CO2 emissions.
Decoking must be performed regularly before tubing reaches its maximum design temperature. This requires shutdown of the unit for mechanical pigging or reduced throughput for online spalling, leading to huge economic losses in all refineries.
Tubacoat’s chemical inertia and smooth surface slows the formation of a solid coke layer when applied to the inner surface of tubes, extending run lengths between decoking threefold and reducing fuel consumption.
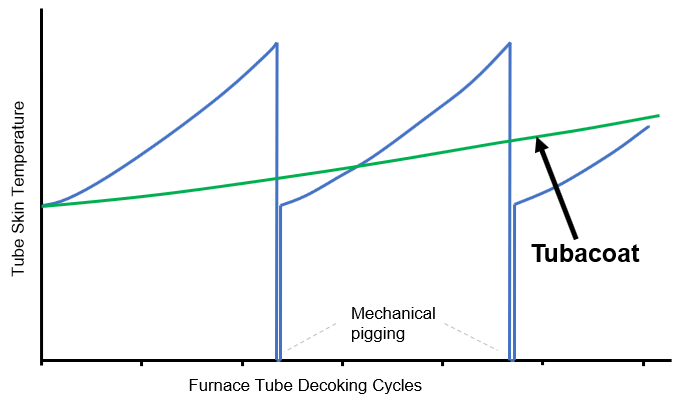
Savings of $3-8million/year
Depending on type of unit, capacity and current decoking frequency
Increased safety and reliability
By reducing number of shutdowns and start ups and avoiding hotspots
Tubacoat also has excellent abrasion and thermal shock resistance to withstand spalling and pigging when needed.